VENT TYPE EXTRUDERS
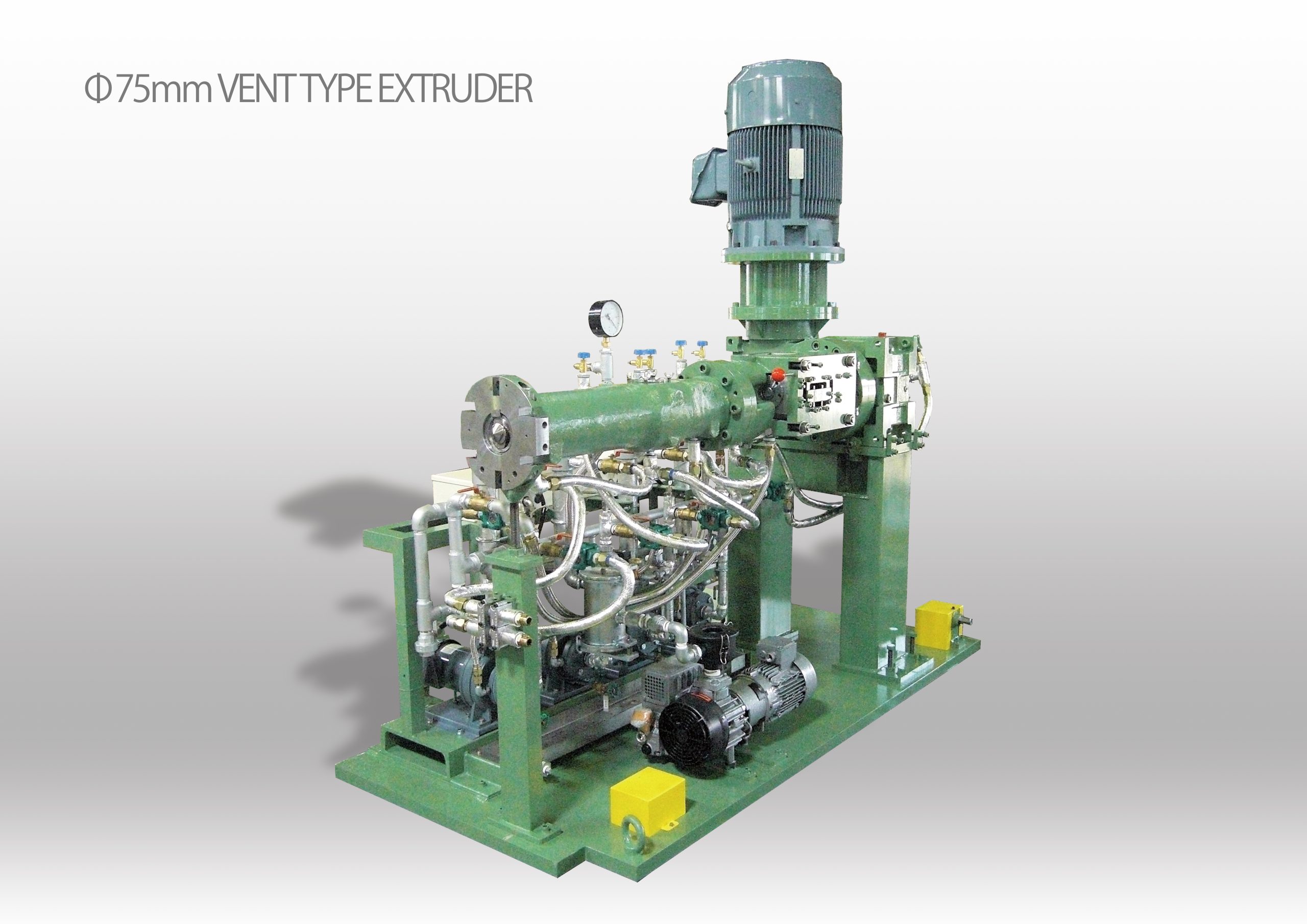
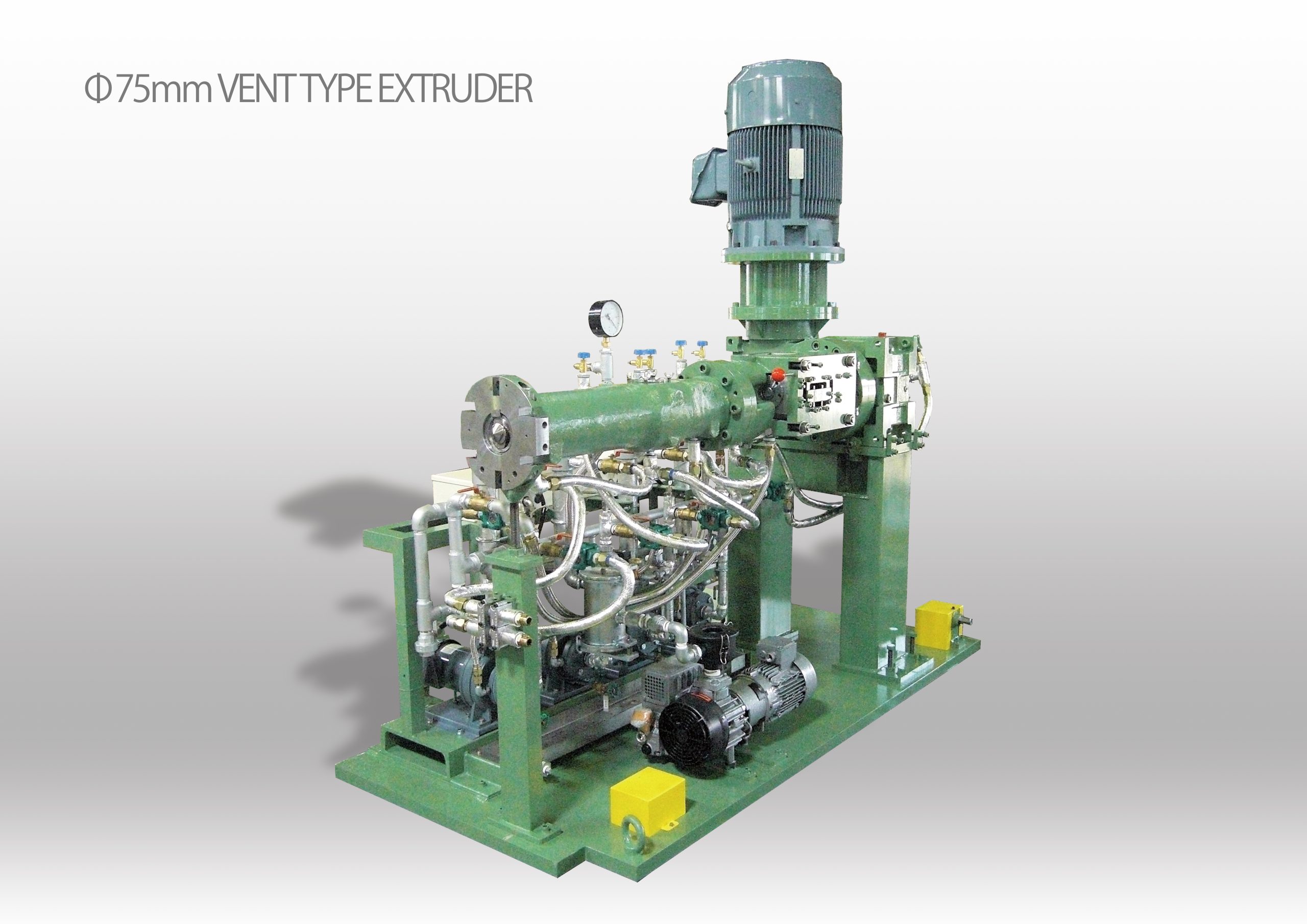
Overview
A mechanism of extruder works in this way: material rubber is charged at a root area of an elongate screw engaged in a cylindrical barrel, then plasticized by heat, kneaded and mixed while being transferred by screw rotation, and then pressurized against mouthpiece at the screw tip area and pushed out through it with a designed profile continuously.
We, Nakata Engineering, have manufactured the extruders majorly as a long-established maker of the rubber processing machinery and kept studying for further developments. We have provided to the market a “hot feed” extruder traditionally, then developed a “cold feed” type which can process material rubber at an ambient temperature, a “vent” type which can degas the trapped air in the processing rubber, and a “pin” type which realized higher output, in our long history. We are proud of our contribution to the advancement of the extrusion technology.
VENT TYPE EXTRUDERS
Single screw vent type extruders have screws of an original and unique design. The primary components of each machine are an extruder unit, a temperature control unit, a drive monitor, a temperature control panel, and vacuum pump.
- 1) Compound can be cold fed to the feed section.
- 2) A single, specialty geometry screw and vacuum pump completely vent bubbles out of extruded components.
- 3) Depending on the type of compound, the screw can be replaced quickly when necessary.
- 4) Because there is minimum of revolving or connecting parts, the costs of upkeep are kept low, and the machine is easy to inspect and maintain.
- 5) Requires a small floor area.
- 6) An automatic temperature control unit, with a circulating pump, controls cylinder temperature to within ±1 degree C, so the shape and size of the extruded products are uniform.
Specification
Related products
-
The most suitable equipment to produce rubber prof……
-
The most suitable equipment to produce rubber prof……
-
Variety of Our “Extruder” Peripheral Equipment
EXTRUDER EXCLUSIVE/PERIPHERAL EQUIPMENTS & DEV……
-
EXTRUDER EXCLUSIVE/PERIPHERAL EQUIPMENTS & DEV……